Understanding Planned Downtime and How to Manage a Downtime Schedule
How often have you been in the middle of work when suddenly your machine crashes? If you’re anything like the rest of us, the chances are you’ve experienced unexpected downtime of a server or machine on multiple occasions – often leading to countless headaches and pulling hair out over lost work or a pause in service. There are many ways you can minimize downtime, but sometimes it’s inevitable and planned or scheduled downtime is necessary.
Planned downtime aims to prevent this from happening while ensuring your machines and service are at optimal functionality at all times. By effectively managing and scheduling downtime to install upgrades and perform regular maintenance, you can help avoid the hassle and financial hit of unplanned downtime.
Planned vs. Unplanned Downtime
Unplanned downtime (also known as unscheduled downtime) is when a lapse in operations occurs because of an unplanned machine or server error. It’s outside your control and doesn’t abide by your company schedule. An example of unplanned downtime could range from a local computer crashing due to a hardware issue to an entire service unexpectedly being down or unavailable to users.This unplanned downtime rarely happens at a time that’s convenient for the company. It can also be quite costly or result in a bad reflection on your brand. Unfortunately, when something happens suddenly and is unexpected, it can often take longer to resolve and get services back up and running.
On the other hand, scheduled downtime, or planned downtime, is when you schedule these down periods at a time that is convenient to the company and minimizes any negative impact for the users. It’s scheduled, proactive maintenance that allows you to install upgrades and perform routine maintenance in order to ensure optimal functionality of your machines and services. This can include replacing old or outdated machine parts, performing regular system updates and patches, and a wide range of other tasks intended to increase reliability of your services.
What is Fixed and Flexible Downtime?
When it comes to planned downtime, there are two ways of scheduling. Fixed downtime adheres to a set schedule – you determine a specific start and stop time for the maintenance to occur. Flexible downtime is more of a window of time during which downtime will happen, though the exact start time is unknown. For example, you may plan for a service being unavailable for 20 minutes at some time between 10p.m.-11p.m., but there is no hard-specified start.
How to Effectively Manage Planned Downtime
Planned downtime is a great way to proactively maintain and upgrade your assets and services while minimizing unexpected issues and unplanned downtime. Each company should manage planned downtime in a way that best suits its needs and production cycle.
When managing your scheduled downtime, there are five important things to keep in mind:
- Know the best windows of time for planned downtime based on your company’s production cycle. Most often, planned downtime is done during after hours or a night shift when machines are not in use. However, if there is no night shift or you have a 24/7 production cycle, you’ll need to figure out the most convenient time to perform maintenance. This could be during slower or off hours.Pro Tip: Scheduling downtime right before major holidays or severe weather can help avoid downtime caused by increased usage or server outages.
- Prioritize all your assets and know which should be handled first. For example, you may know that a certain computer is always acting up and therefore devote more time to maintaining this individual machine.
- Implement clear guidelines and well-defined standard operating procedures (SOPs) for each repeated operation. This will help ensure tasks are performed correctly and that no steps are missed. Clear SOPs can also benefit newer team members who aren’t as experienced performing some of these maintenance tasks. Using tools like runbooks can help to streamline repeated tasks during scheduled downtime in order to streamline the process and minimize the amount of downtime needed to complete all operations.
- Know your problem areas and remedy any known bottlenecks and constraints. When you know your areas of weakness, it becomes much easier to diagnose them. For example, if you regularly have delays in the production process when developing a particular service or application, you can make sure to plan ahead and ensure these processes are expedited in order to stay within a timeline or deadline.. Other examples of common problem areas include older machines, which can be remedied with additional inspections; or new or inexperienced employees, who can benefit from being paired with senior level team members, additional training, or well-kept runbooks.
- Encourage a more collaborative culture! Collaboration between departments like maintenance and IT operations or development can help create smoother workflows and cut back on any unnecessary roadblocks or slowdowns. When production teams are aware and considerate of what maintenance does, they can prepare their work stations ahead of planned downtime to ensure the maintenance team is able to quickly and effectively complete their job without distractions.
Scheduling downtime is a great way to ensure optimal functionality of your machines, increase credibility of your services, and minimize any occurrences of unplanned downtime in the future. Learn more about how PagerDuty can help your teams increase reliability and minimize the need for downtime by signing up for a 14-day free trial.
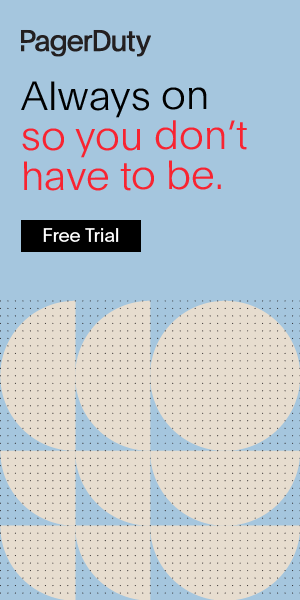
Additional
Resources
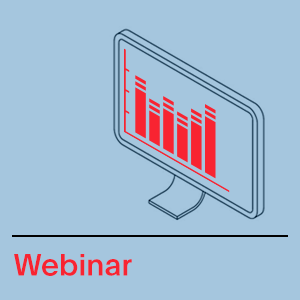
Webinar
PagerDuty Deep Dive: How to Optimise Your Digital Ops Platform
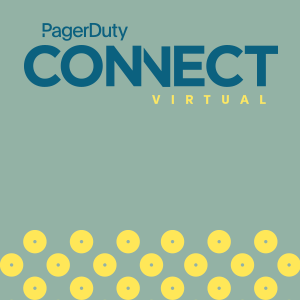
Webinar
PagerDuty Connect: Challenges in Real-Time Ops